Optimizing Metal Product Design: A Comprehensive Guide Using SolidWorks, Autodesk Fusion 360, Simulation, and Programming Software
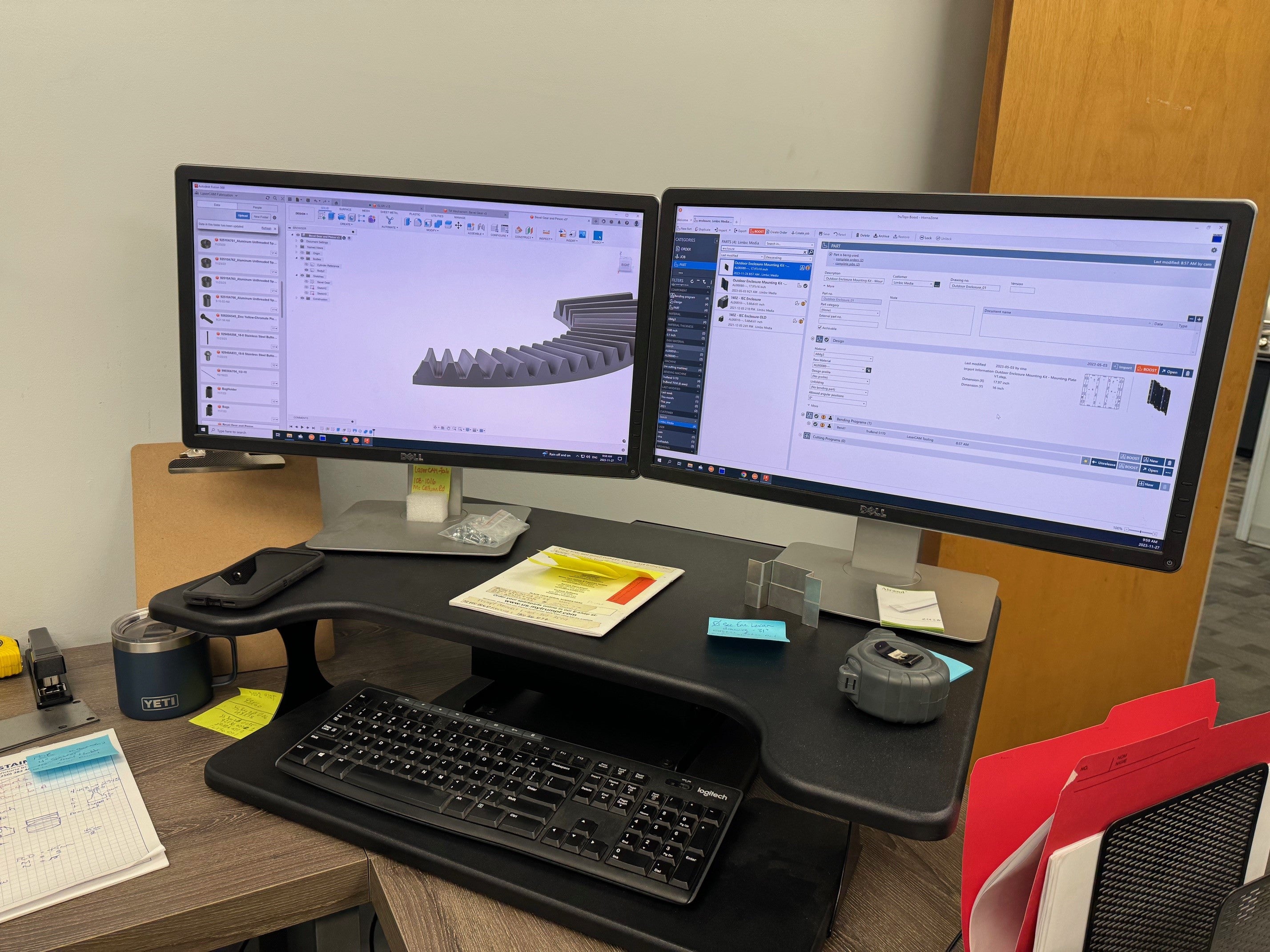
Introduction:
In the realm of metal product design, leveraging advanced design software is crucial for achieving precision, efficiency, and sustainability. This blog post will delve into the utilization of powerful tools such as SolidWorks and Autodesk Fusion 360, along with simulation and programming software, to streamline the design process, ensure structural integrity, and minimize material waste.
1. Designing with SolidWorks and Autodesk Fusion 360:
1.1 SolidWorks:
SolidWorks is a versatile 3D CAD software widely used in the manufacturing industry. It enables engineers to create detailed 3D models of metal products, offering a comprehensive suite of tools for parametric design and assembly.
-
Parametric Design: SolidWorks allows for parametric modeling, where dimensions and features can be easily modified, ensuring flexibility throughout the design process.
-
Assembly Modeling: Assembling intricate metal structures becomes seamless with SolidWorks, providing a clear understanding of how individual components fit together.
1.2 Autodesk Fusion 360:
Fusion 360, a cloud-based 3D CAD, CAM, and CAE platform, complements SolidWorks with additional capabilities.
-
Cloud Collaboration: Fusion 360's cloud-based nature facilitates real-time collaboration among team members, allowing for concurrent design and analysis.
-
Integrated CAM: Fusion 360 seamlessly integrates computer-aided manufacturing (CAM) tools, enabling the generation of toolpaths for CNC machining.
2. Simulation for Structural Integrity:
2.1 Bend Deduction Analysis:
Simulation software from developers such as Trumpf, plays a pivotal role in predicting the behavior of sheet metal during bending processes.
-
Bend Deduction Calculations: By simulating the bending process, these tools provide accurate bend deduction values, ensuring precise fabrication and minimizing the risk of flaring or deformation.
-
Hole-to-Bend Analysis: Simulation software helps evaluate the impact of hole placement in relation to bends, preventing interference and maintaining structural integrity.
3. Programming Software for Efficiency and Sustainability:
3.1 Optimizing Sheet Metal Usage:
Programming software, like Trumpf's TruTops boost, can be employed to create algorithms that optimize sheet metal usage.
-
Nesting Algorithms: These algorithms ensure efficient layout of components on a sheet, reducing waste and maximizing material utilization.
-
Recyclability Considerations: Programming tools help in designing for recyclability, ensuring that leftover material can be easily recycled, contributing to a more sustainable manufacturing process.
Conclusion:
In conclusion, the integration of SolidWorks and Autodesk Fusion 360, coupled with simulation and programming software, empowers designers to create metal products with precision, structural integrity, and minimal environmental impact. By leveraging these tools, engineers can optimize every aspect of the design process, from initial modeling to final fabrication, resulting in efficient use of materials and a more sustainable approach to manufacturing.